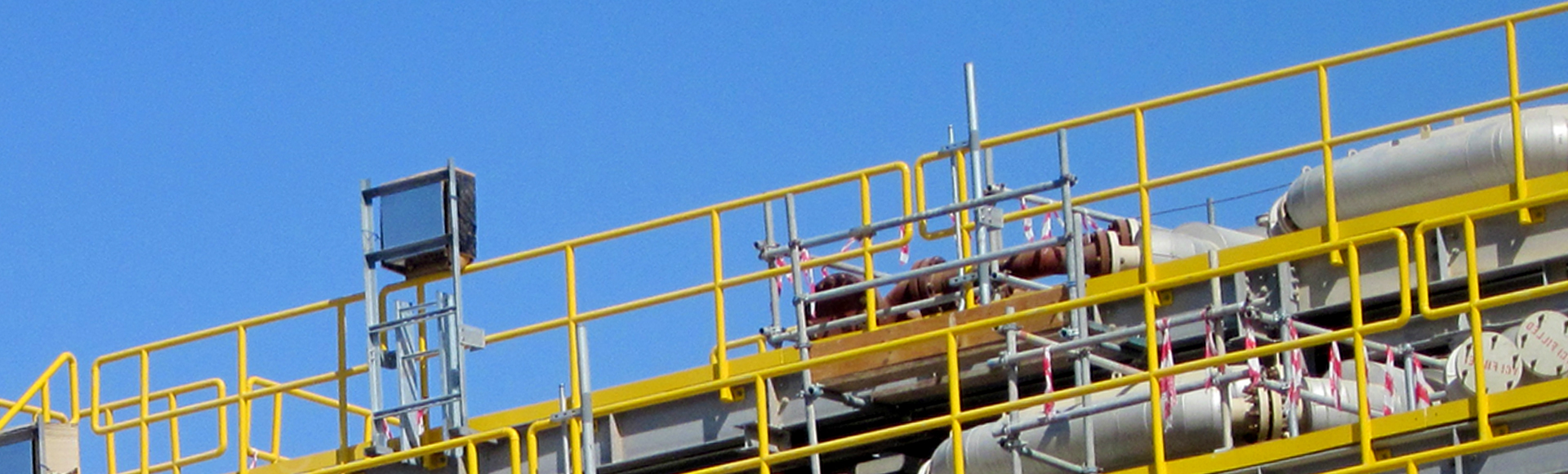
Alumina Tube Digestion
Tubular heating for digestion of boehmitic bauxite
Reduced OPEX and O&M
15% energy savings
7% capital savings
Reduced downtime means higher availability
Challenges
Solutions
Benefits
Related projects
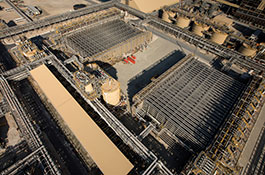
Al Taweelah alumina refinery
United Arab Emirates (UAE)
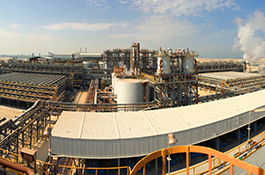
Ma'aden Alumina Refinery
Saudi Arabia
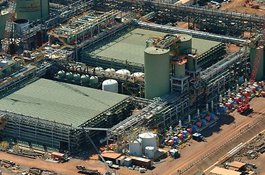
Yarwun Alumina Refinery
Australia
Related services and technologies
Technical papers
ICSOBA2013 September 2013, conference hosted in Krasnoyarsk, Russia
Application of Tube Digestion Technology to Non Ferrous Metals Industry
Conference Of Metallurgists 2012 (COM2012). Presented October 2, 2012
Pressure Surge Mitigation at High Temperature Tube Digestion Facility
9th AQW Conference (International Alumina Quality Workshop), Perth, Australia, 18-22 March 2012
All Technical Papers
News
孵化and URPS embark on South Australia's Climate Ready Coasts Program
Wednesday, October 25, 2023