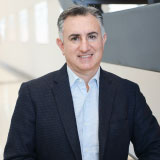
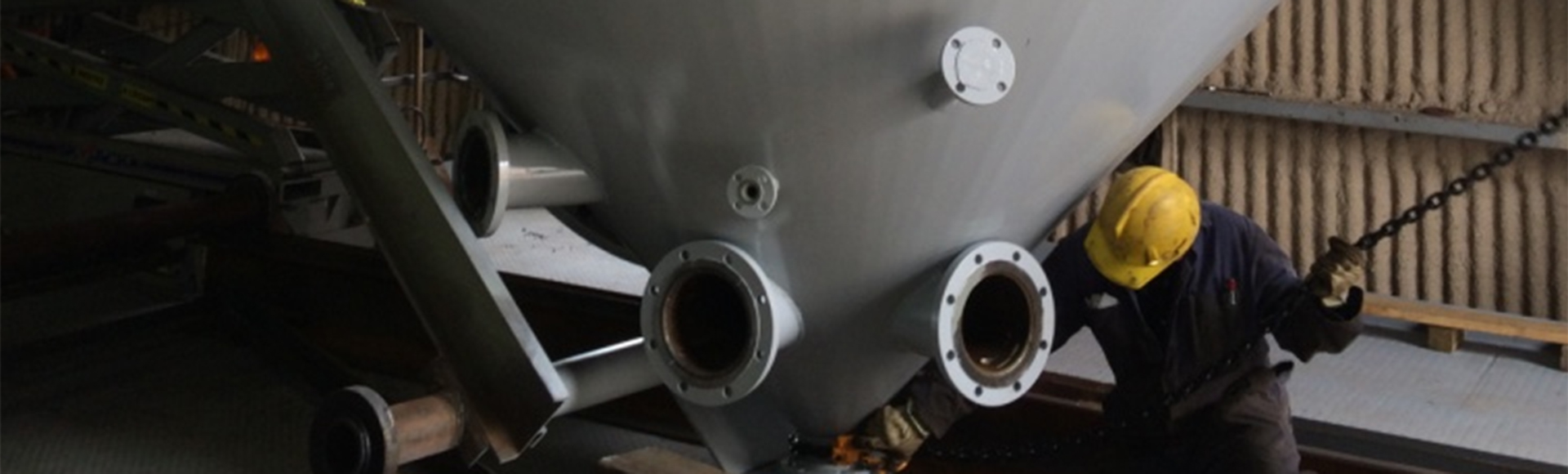
Fluidized Bed Systems
Custom fluidization design for novel processes & unconventional applications
Increased
Capacity
Custom
equipment design
>800°C
high-temperature process vessels
Feedstock
flexibility
Solutions
Benefits
Related projects
Related services & technologies
Technical papers
Impact of gas distributor on hydrodynamics in a cold flow annular dual fluidized bed for pressurized chemical looping
Presented at FBC24 2022, Session 6B.
Natural graphite purification through chlorination in fluidized bed reactor
Extraction 2018, August 26–29, 2018 • Ottawa, Ontario, Canada
Gold Concentrate Roaster for Sulphur Carbon and Arsenic Removal
Conference of Metallurgists, September 30, 2014
All Technical Papers
News
孵化and Tractebel join forces to support nuclear developments in North America and Europe
Wednesday, August 30, 2023