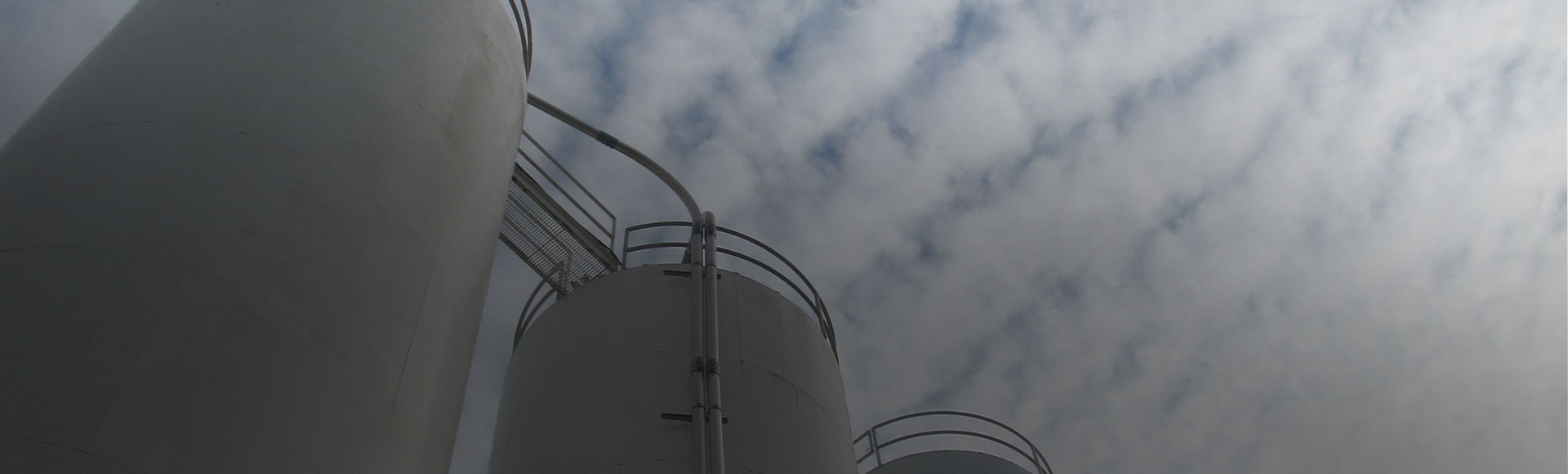
PneuCalc
A powerful design and optimization software for your pneumatic conveying systems
Design and troubleshoot pressure and vacuum systems
Calculate and display dilute, dense, and mixed modes of conveying
Debottleneck and verify design parameters instantly
Easy-to-use drag-and-drop features
“I have used PneuCalc 7.0 to help verify, set up, and troubleshoot various pneumatic conveying systems. It was quick and easy giving the guidance needed for each project. This software will be another great tool for anyone that wants to understand the specifics of their pneumatic system airflow.”
Ready to optimize your system?
Take control of your material flow and maintain your system assets now.