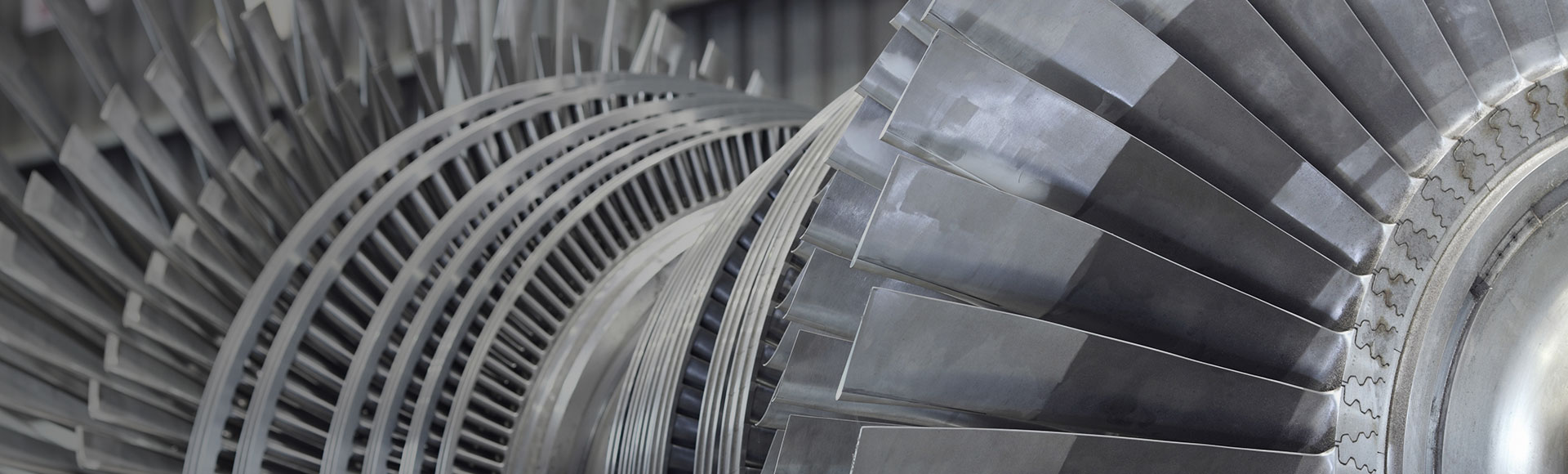
Al Taweelah Alumina power and steam integration
Supplying combined-cycle power to the Al Taweelah alumina refinery
Emirates Global Aluminium (EGA) | United Arab Emirates | 2015-2018
Combustion turbine and heat-recovery steam generator added
First steam delivered in2018
Enough power to manage531 t/hof high-pressure steam at the refinery
7 million hours workedwithout a lost time incident
Challenges
目前阿联酋铝业(EMAL)电厂has eight combined cycle gas turbines (GE 9F.03), one simple cycle gas turbine (GE 9F.03), and four steam turbines. A total of 3,000 MW of power supplies aluminum potlines at the EMAL smelter.
EGA is expanding its EMAL combined-cycle power plant to supply both steam and power to a new alumina refinery. This must be completed in time for the refinery commissioning and ramp-up.
This project includes many brownfield work fronts, including the conversion of the existing simple-cycle combustion turbine to a combined cycle one. This will be completed during a scheduled outage.
The integrated power plant must be capable of managing an instantaneous full-load reduction at the alumina refinery of 531 t/h of high-pressure steam.
Solutions
As the EPCM contractor, we are integrating a new power block with the existing power plant and supplying steam, power, and utilities to the refinery.
The integrated power plant can supply steam to the refinery from several heat-recovery steam generators (HRSGs), improving the availability and operational flexibility of the plant.
The Hatch and EGA project teams integrated seamlessly to manage issues relating to the brownfield interfaces.
To reduce a full load of 531 t/h high-pressure steam at the alumina refinery, the power plant was equipped with a steam-management system. This prevented the HRSGs from tripping or having the safety valves lifted, while balancing the power-plant load to reach a steady-state operating condition.
Highlights
The integration of power and steam involves the addition of a GE 9F.05 combustion turbine and heat-recovery steam generator. As well as converting the simple cycle unit to a combined one, a condensate treatment center, a new water treatment plant, and all required utility interconnections were built, installed, and managed.
To deliver the project on time and on budget, the work was carried out globally, with the site team in the United Arab Emirates being supported by engineering offices in South Africa and Canada, as well as subject matter experts from Australia and subcontractors in India.
The integration allows for the utilization of ten gas turbines, ten heat-recovery steam generators, and four steam turbines in numerous configurations to meet constantly changing demands for power and steam.
The alumina refinery delivered the first steam in October 2018.
Project numbers
Gross capacity of the EMAL power plant after completion will be3.5 GW531 t/hof high pressure steam
81 t/hof low pressure steam
10gas turbines
10heat-recovery steam generators
4steam turbines
What's your challenge?
Related Projects
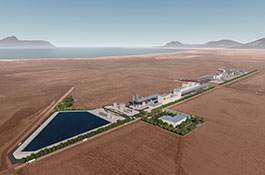
Imperial Valley, California, USA
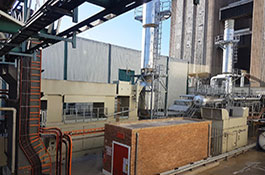
South Africa
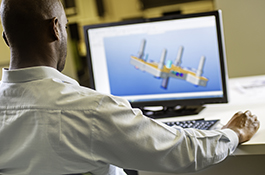
United States
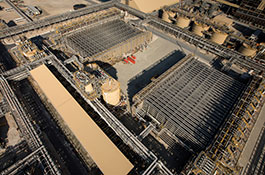
United Arab Emirates (UAE)
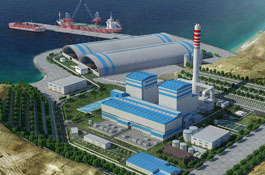
Turkey
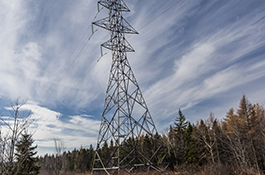
Canada
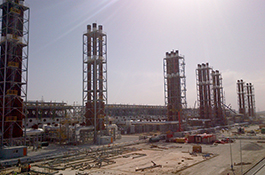
Jordan
See All