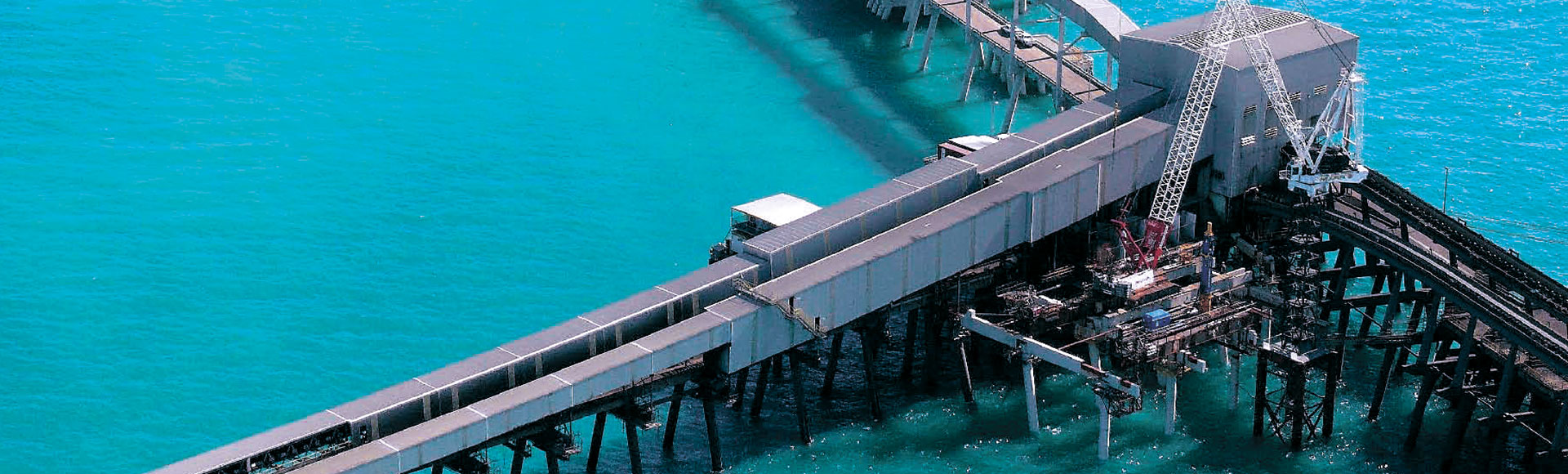
Dalrymple Bay Coal Terminal 7X Project
Improving capacity as daily business continues
DBCT Management Pty Ltd. | Australia | 2005-2009
3rd largest terminal in the worldat time of completion
~50% increase in capacityto 85 million-plus tonnes per annum
1,100 workersin construction at project peak
AUD$1.26 billion,the largest construction program in the terminal’s history
Challenges
- Provide engineering and project management solutions that allow for easy construction within a fully operational facility, with minimal disruption to current activity.
- Carefully integrate multiple disciplines and stakeholder requirements.
- Include a third inloading system, a stockyard expansion, a third outloading system and a fourth berth.
- Upgrade major power and control systems, and provide additional controls to reduce the impact of noise and dust emissions.
Solutions
- The stockyard volume was increased by 43% within the same terminal footprint.
- 创新的版本tical concrete bund walls and two additional stockpile rows improved reclaiming efficiency.
- Automated wagon vibrators were implemented to eliminate manual handling and noise-related health and safety hazards.
- Jetty was widened on a single row of vertical piles to reduce cost and improve constructability.
- The new outloading system included a full 3D anti-collision avoidance system for the yard machines, significantly increasing efficiencies for the stacking and reclaiming operations.
Highlights
- Winner, Queensland Engineering Excellence Award – Industrial Development and Manufacturing Engineers Australia, 2010
- Winner, 2009 Products and Manufacturing Facilities Excellence Award, Engineers Australia
- Throughput capacity for all major components of the inloading and outloading materials-handling systems reached nameplate capacity almost immediately after commissioning.
- During the project’s peak, approximately 1,100 workers were involved in construction, many of whom were mid-tier local contractors, which boosted the local economy with employment opportunities.
Project Numbers
5.5million total project hours worked.Approximately1,100workers involved in construction at the project’s peak.
AUD$1.26 billiontotal project cost.
Aurecon Hatch managed safety for the construction activities on site, and completed the project with a lost-time injury frequency rate (LTIFR) of 0.92.
What's your challenge?
Related Projects
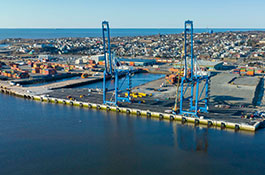
Westside Modernization Project
Saint John, New Brunswick, Canada

Port Expansion Project - Customs Free Zone Argos
Cartagena, Colombia
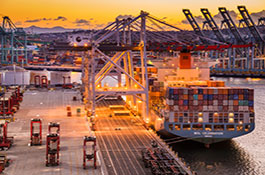
TraPac Terminal Automation Support
United States
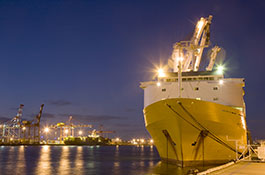
Fremantle Container Terminal
Australia

Drayton South Open-Cut Coal Mine
Australia
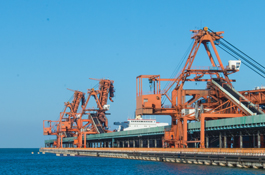
Transnet Capital Expansion Program
South Africa
See All