
Port Expansion Project - Customs Free Zone Argos
Argos to triple its export capacity from Cartagena
Zona Franca Argos S.A.S | Cartagena, Colombia | 2018-2022
$42 millioninvestment in port infrastructure
High technological and environmental standards to lower particulate matter emissions below20 mg/Nm3
Project employed approximately1,200people
Challenges
- Provide timely, cost-effective, sustainable solutions that assist Argos in constructing a new port terminal that will triple its capacity to receive and export products
- The new terminal will substantially increase cement exports to the United States, taking advantage of the growing demand for construction materials in that country
- The project requires civil, electrical, mechanical, and automation and control work while maintaining current operation with minimum downtime
- 使用技术来减少大气排放to comply with both the environmental and legal requirements, as well as the BASC, OEA and ISPS requirements
- Taking the necessary safety precautions to keep the construction project on schedule despite the COVID-19 pandemic
Solutions
- Oversaw the integration of all disciplines and equipment suppliers
- Integrated local engineering performed by the civil designer
- Provided detailed mechanical, electrical, and instrumentation and control engineering
- Delivered innovative plans, reports, dynamic simulations, 3D models, and CAPEX elaboration
- Supported review of information and structures in the field and performed the inspection of the equipment received by the project’s main supplier
Highlights
- The new terminal will offer a loading rate of 1,200 tons per hour for cement and 900 tons per hour for clinker
- More than 16,000 Hatch hours were invested in engineering activities across all disciplines
- Technical support in the field, and inspection of equipment delivered by the main supplier of the project, added value to the client for the development of the project
- At the completion date, this megaproject will have used more than 10,000 cubic meters of concrete, 1,200 tons of reinforcing steel, about 5 kilometers of piling, and will have installed 2,658 tons between equipment and metal structure
Project numbers
$42 million750,000man-hours, more than16,000Hatch hours invested
1,200employed throughout the entire project
Draft of12.8meters
Reduced emission below20 mg/Nm3
Export volumes of cement and clinker up to3.5million tons per year
New terminal152meters long by18meters wide
Vessels of up to60,000deadweight tons
Access walkway170meters long
One-kilometer-long tubular strip
Loading rate of1,200tons per hour for cement;900tons per hour for clinker
Used more than10,000cubic meters of concrete,1,200tons of reinforcing steel, about5kilometers of piling
Will have installed2,658tons between equipment and metal structure
Having Hatch’s support during all stages of the project was key to its successful completion. Their support facilitated integration of all stakeholders such as equipment suppliers, construction and erection contractors, even while a COVID pandemic arrived in the middle of the execution. Project management services also guaranteed good control of schedule, cost and documentation during a very sensitive part of the project.
How we can help you
If you have a problem that needs to be solved, please get in touch.
Related Projects
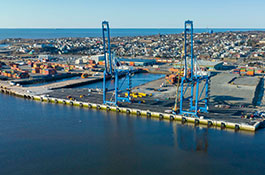
Westside Modernization Project
Saint John, New Brunswick, Canada
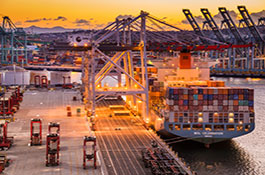
TraPac Terminal Automation Support
United States
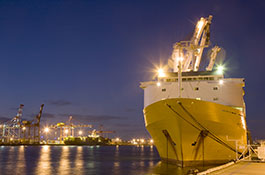
Fremantle Container Terminal
Australia
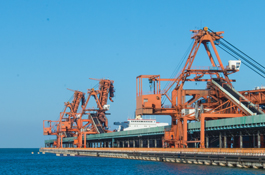
Transnet Capital Expansion Program
South Africa
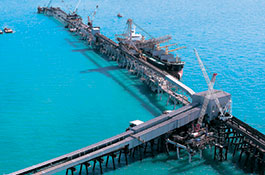
Dalrymple Bay Coal Terminal 7X Project
Australia