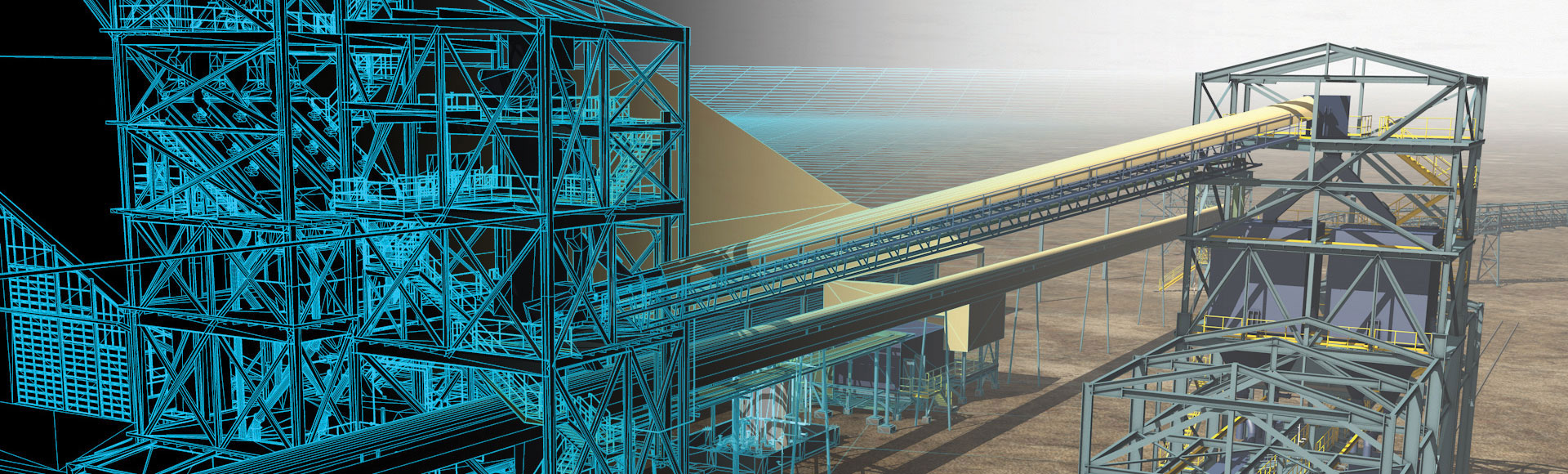
Faustina Brownfield Fertilizer Plant
The Mosaic Company | United States | 2010–2012
30 days
of downtime avoided
3D modeling
for precise design in tight spaces
Challenges
- Mosaic needed to convert its diammonium-phosphate (DAP) production plant to accommodate a new product: its next-generation MicroEssentials® fertilizer.
- The company wanted to add this new MicroEssentials® production capability while maintaining its current monoammonium-phosphate (MAP) and DAP production.
- The plan was to modify the existing “C” production train at its Faustina, Louisiana facility, a project that required significant expansions of the product storage, load-out, and rail systems.
Solutions
- Mosaic benefited from having just one company deliver full engineering services for the project, from the conceptual study phase right through detailed design, construction, and commissioning.
- Both the design and installation work for screening and rail load-out facilities were conducted by expert 3D modeling engineers.
- 新旋风除尘器和raw-material-feed systems were fabricated as discrete units and lifted into place atop the existing plant structure where they were installed.
- This process saved two weeks of construction time and minimized associated costs, crane time, safety risks, and plant downtime.
Highlights
- The brownfield work was executed without interrupting plant operations.
- Personnel worked 7,895 on-site hours with no safety incidents.
- By combining screen elevations and orientations to fully utilize the available area, at least 30 days of production downtime for the installation work were saved.
- The high-efficiency approach was very effective. Just four hours after plant start-up, the new MicroEssentials® fertilizer was meeting product specifications.
“Their leadership in the commissioning efforts of this project.... They expanded their role to include construction coordination to see that the system was brought online in as timely a fashion as possible due to the situation at hand. Their services were exemplary.”
Project numbers
US$80 millioncapital value7,895on-site hours with 0 LTIs